Refrigeration Package
Refrigeration Package
Browse Other Oil & Gas
Technologies
- Storage Tanks
- Refrigeration Package
- Pressure Swing Adsorption
- Flare Gas Recovery Package
Our Services
Download (.PDF,250KB)
Catalog 2021
Download (.PDF,250KB)
Product presentation
Watch
Latest promo video
Refrigeration Packages in Oil and gas Industry
In terms of strategic importance, the refrigeration industry is an infrastructure industry that plays an important role in numerous industries and industrial processes. The petrochemical, chemical, and oil refining industries require large-scale refrigeration systems. Among the important processes that require refrigeration in these industries are:
Separation of gases by liquefaction of a gas
Condensing exhaust gases from a liquid tank
Storage of liquids at low temperature
Moisture control of hygroscopic materials
Solidification of matter from solution
Heat removal in chemical transformations
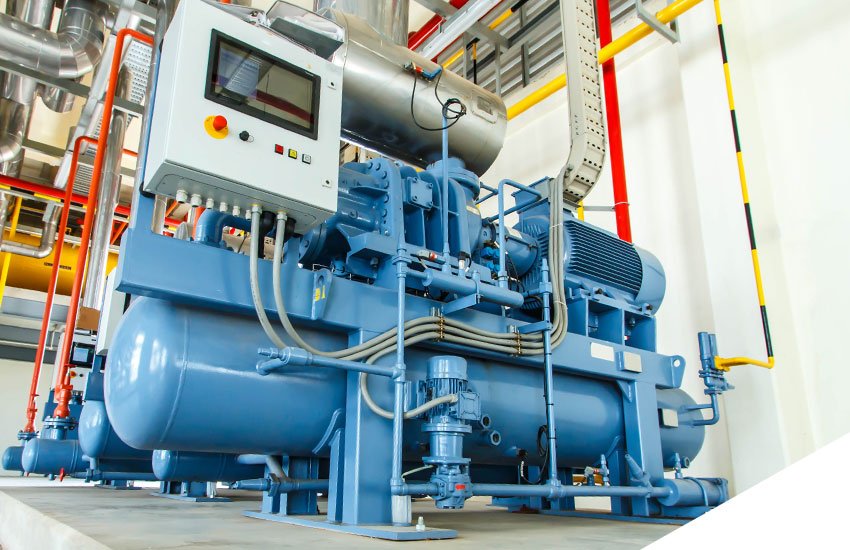
1. Refrigeration Cycle
The conversion of refrigeration involves taking heat from the refrigerant and transferring it to matter at a lower temperature than the refrigerant. First, the refrigerant gas enters the compressor. The refrigerant gas is compressed by the compressor, resulting in not only compression but also an increase in temperature. Through the mentioned pipes, this hot gas is sent to the condenser. Condensation occurs in the condenser, which results in the transformation of hot, compressed gases into high-pressure liquids. Accordingly, in this case, the outlet of the condenser, which is the high-pressure liquid, moves towards the expansion valve. Pressure is reduced on the expansion valve at high speed, and the result is a mixture of cold liquid and low-pressure steam at the output.
Evaporation is the final stage of the refrigeration cycle. This component is responsible for heating the cool liquid that has emerged from the expansion valve. In this way, the refrigerant has been re-evaporated and is ready to be reinserted into the cycle.
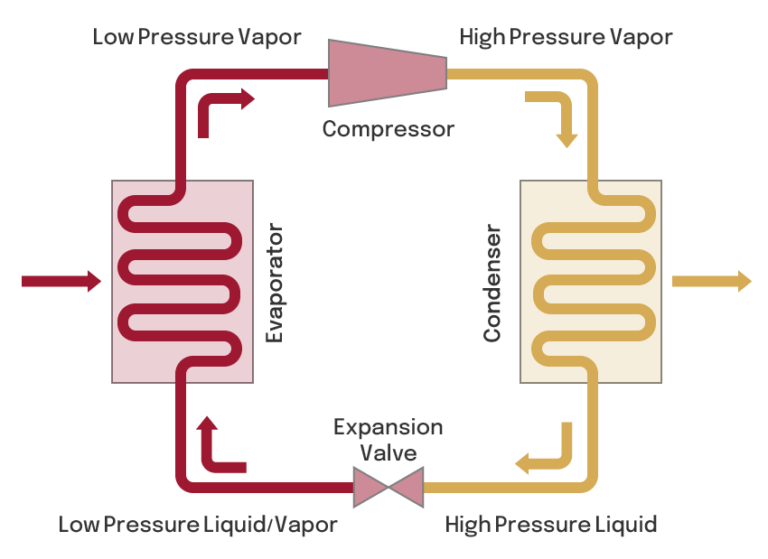
The operating temperature of these refrigeration packages is one of the most important characteristics that distinguish them from one another. The temperature may range from -70 degrees Celsius to 15 degrees Celsius.
According to the cooling stages, the systems may be classified as single-stage or multi-stage. Below is a comparison of these two approaches:
Single-stage refrigeration systems
In a single-stage refrigeration system, the condensation from low to high pressure occurs in one step. The following image illustrates the schematic of this process:
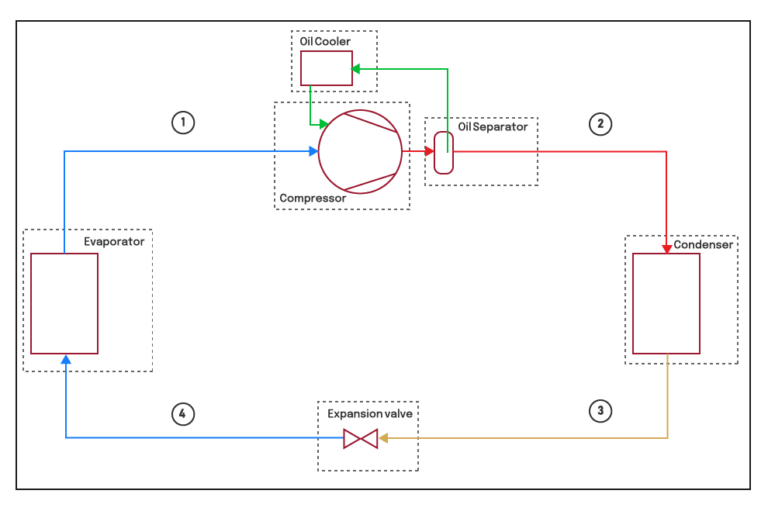
Refrigeration systems with two or more stages
A multi-stage refrigeration system includes more than one stage of gas compression. Industrial multi-stage refrigeration systems employ intercoolers in the compression stage to cool exhaust gases from the first stage. As a result of cooling the exhaust gas from the LP compressor, it is also possible to regulate the temperature of the HP compressor. Through the expansion of liquid refrigerants, intercoolers provide cooling. Multistage coolers are used when there is a large difference between the evaporating and condensing temperatures, resulting in high condensation ratios and other adverse conditions. Below is a schematic representation of this process. The economizer is used to cool the refrigerant after the condenser, as shown in the picture.
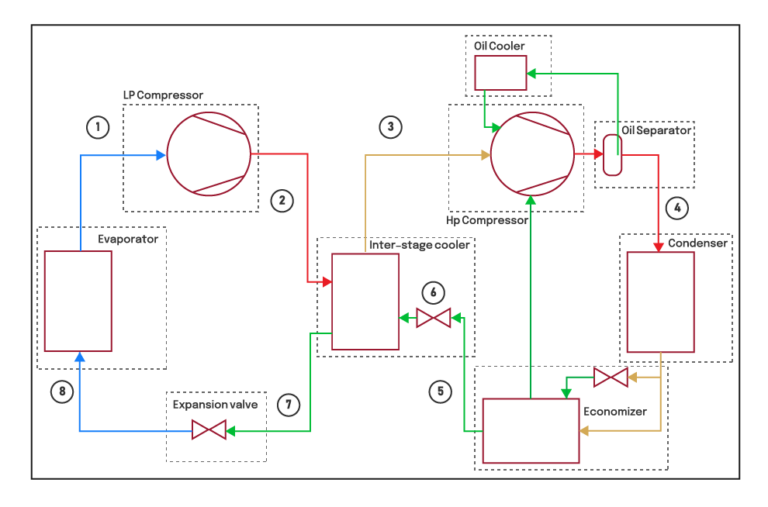
2. Refrigerants
Refrigerants are an intermediate fluid to transfer heat and energy from the evaporator to the condenser. It is important to select the appropriate refrigerant for the operational and process conditions because different refrigerants have different thermodynamic properties, such as latent heat of evaporation, density, and critical point. In addition to the operating conditions, other parameters will also influence the choice of refrigerant. Among these parameters, safety issues and environmental effects should be considered when selecting a refrigerant.
A list of the most common refrigerants and their specifications can be found below.
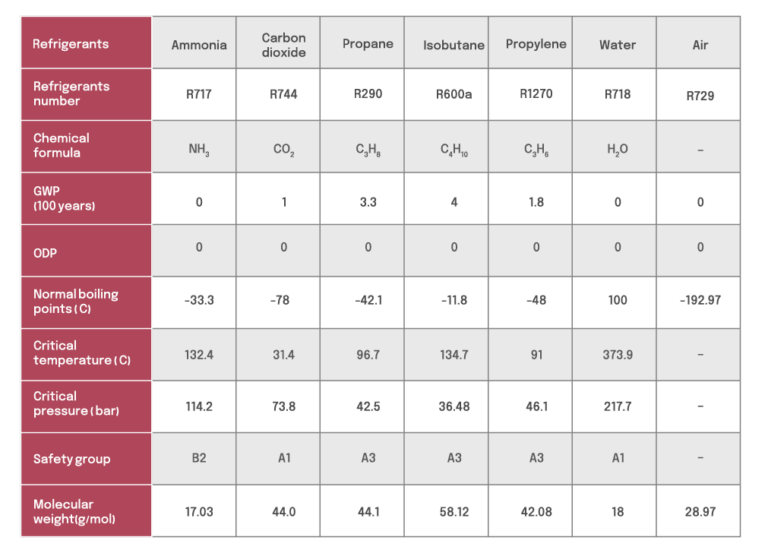
3. Components of Refrigeration Systems
a. Main components
Refrigeration systems consist of four major components: compressors, condensers, evaporators, and expansion devices. Each of these components performs a specific function.
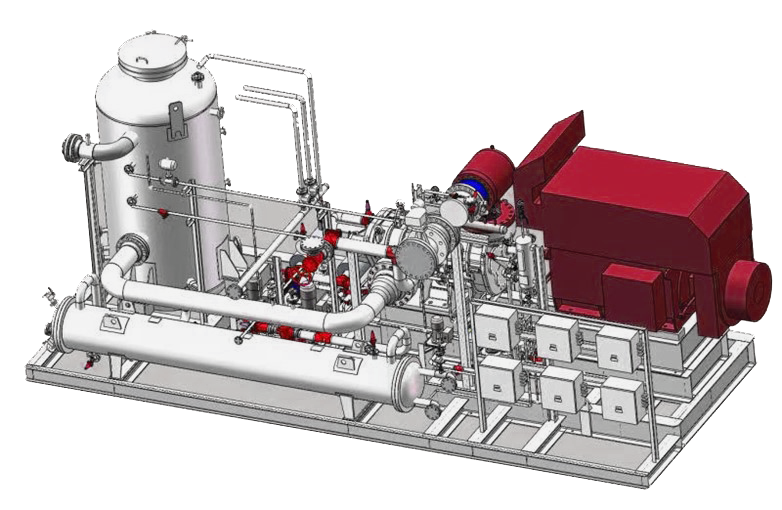
Compressors:
A compressor in a refrigeration package is responsible for compressing refrigerant. The compressor is the heart of a compression system, and the most commonly used ones in coolers are:
1) Rotating
2) Centrifugal
3) Reciprocating
The refrigeration industry is dominated by screw compressors, which are rotary compressors.
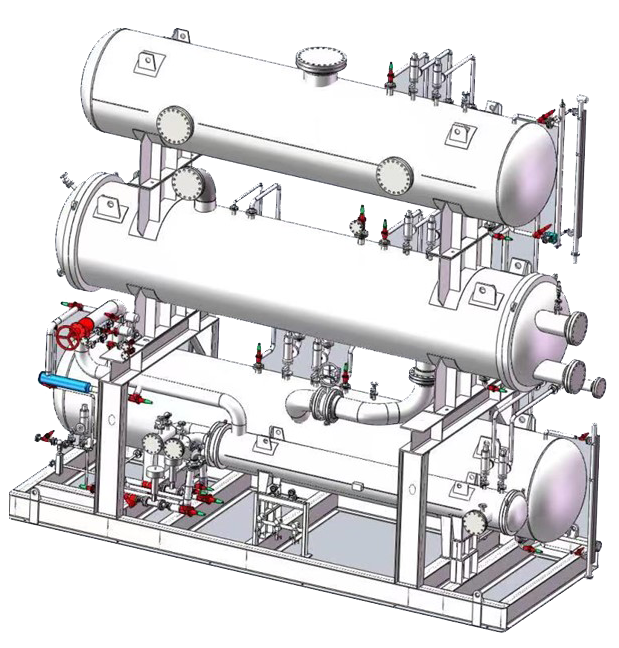
Condenser:
Condensers are heat transfer devices in which the heated refrigerant vapor is transferred to the distillation agent through the surface of the pipes, causing the vapor to cool to its saturation temperature and then turn into a liquid. Most distillation processes rely on either air or water or a combination of both.
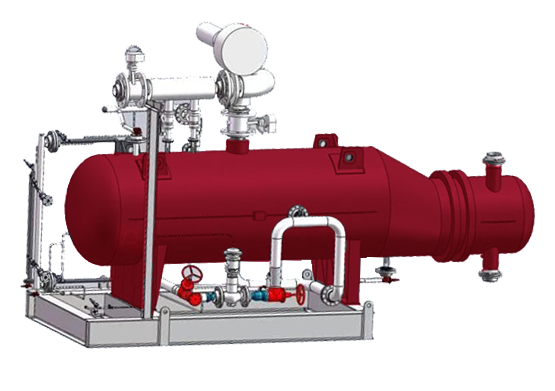
Evaporator:
The term ‘evaporator’ refers to any surface that evaporates a cooling substance and transfers heat to a space or body. In the evaporator, the refrigerant enters at a lower temperature than the target environment and evaporates due to heat absorption and cools the material. Evaporators may be used to cool water, air, or other types of liquids and gases.
Expansion Valve:
This device is an integral part of the steam condensation refrigeration cycle, which is responsible for determining the temperature of the target environment in order to control the amount and temperature of refrigerant entering the evaporator.
b. The lateral components of a refrigeration system
There are also other side components to refrigeration cycles, including:
Oil Returning Equipment:
Lubrication is used to maintain the performance of the compressor. With the refrigerant, the compressor pumps some oil as well. The compressor may expel a large amount of oil, so it is important to return the oil to the compressor as soon as possible. Thus, equipment such as oil pumps, oil separators, oil coolers, and oil filters are used to return the oil.
Economizers:
The economizer is a type of heat exchanger and intermediate cooler. It increases the cooling capacity of the system, increases its efficiency, and reduces the energy loss during the operation of the system.
3. Zeta's capabilities in designing, supplying, manufacturing, installing, and operating cooling systems
The Zirsakht Tadbir Arin Company entered the field of this industry with a view to maximizing its internal capabilities in order to provide industrial cooling packages and transfer relevant technology. Among its main activities are:
Package Design
Engineers at this company have the capability of designing complete package processes, as well as mechanically designing condensers, evaporators, economizers, oil systems based on international standards such as ASME and API, as well as parts of electrical systems, instrumentation, and control systems.
Equipment Procurement
Apart from the compressor and instrumentations, and control systems, for which there is no reliable internal capacity, the remainder of the parts are designed so as to utilize the capacities and quality products of domestic manufacturers. Overall, it is estimated that more than half of the package equipment can be sourced domestically.Apart from the compressor and instrumentations, and control systems, for which there is no reliable internal capacity, the remainder of the parts are designed so as to utilize the capacities and quality products of domestic manufacturers. Overall, it is estimated that more than half of the package equipment can be sourced domestically.
Installation and after-sales services
We believe that installation and commissioning services, as well as timely and high-quality after-sales services, are equally important to the engineering and supply departments of this company. As a result of having operational plans, it uses experts in this field to ensure that respected employers receive high-quality equipment and will not have to worry about setup and after-sales services, including supply of parts and maintenance and repair services.
Single Service
Downloads
Lorem ipsum dolor sit amet, consectetur adipiscing elit. Ut elit tellus, luctus nec ullamcorper mattis, pulvinar dapibus leo. Lorem ipsum dolor sit amet, consectetur adipiscing elit.
- Download bochure (DOC)
- Download bochure (PDF)
- Rules about service apply generally
- Users manual